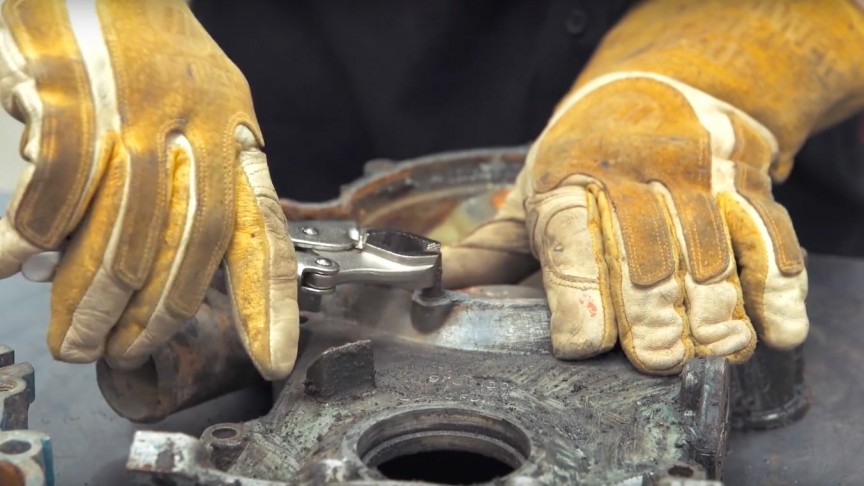
You might want to crunch the numbers including whatever your time is worth and see if simply replacing the part might be better. Then heat the ALUMINUM as quickly as youre able aluminum expands more than stainless when heated and attempt to tighten it to see if you can break it free.
I think as you stated just welding the nut on the bolt end will loosen up the bolt.
Steel bolt stuck in aluminum. Build a little dam around the bolt and pour in a little puddle and keep the casting in a warm place it will take a while days but it will gradually eat away the steel eventually it will loosen the bolt you dont need to get rid of the whole bolt just enough to get it out. I think as you stated just welding the nut on the bolt end will loosen up the bolt. Make sure right after the weld you cool down the bolt immediatly and it will come right out of there.
What happens is the bolt will expand when heated. This is the best way to remove a steel bolt that is in aluminum housing due to oxidation and corrosion. I have been working on the brakes of my L322 TDV8.
When I removed the callper one bolt holding it to the car hub sheared while being removed. The calipers are Brembo cast aluminium so as above I now have a bolt stuck in. Fortunately there is a sizable portion sticking out above the caliper enough to allow me to grip with Mole Grips.
I need to remove a lot of steel bolts from an aluminum engine block they feel like welded in there because the level of rust. Just turning them would crack the part or break the bolts. I wonder whats the bestfast way to remove them with minimum parts damage.
Use a propane torch to heat the bolt. Cut the bolt at almost surface level then. That is very encouraging.
It means that the bolt is stuck in the iron block not clamped in the aluminum by the corrosion product. It might not pull all of the way out yet but if it can move at all it wont be contributing much friction to turning the bolt. Maybe that means the ATFacetone solution can be applied directly where it is needed.
You bet RW any one that has done mechanical work for years has experienced that called dissimilar metals problem. Very common with un-anodized aluminum and steel bolts. Have had some success with torch heating the aluminum use caution as it will let go and melt if you are not careful.
Try tightening just a bit at first and then loosen. Aluminium expands roughly twice as much as steel for a given increase of temperature. That means if it is a steel shaft in an aluminium housing heat is your friend.
For say an aluminium plug in a steel part you want to cool it. If it has corroded or galled you may have a problem. Let it soak as long as you can.
Due to the cracking of the anodized layer when mounting a very little area of unnoble metal the aluminum underneath will be in contact with a very big area of the more noble metal the stainless steel. This will cause galvanic corrosion which can increase tremendously depending on the area of the aluminum. This was part of a suspension Job I did on this G6 where a bolt got stuck in aluminum and much worst than I thought it would be.
I made this part a separate. Aluminum and Stainless wind up effectively cold welded due to galvanic corrosion. Lots of penetrating oil and take your time - soak it good wait soak it again wait soak it again.
Then heat the ALUMINUM as quickly as youre able aluminum expands more than stainless when heated and attempt to tighten it to see if you can break it free. Manifold studs break and most extraction methods include drilling it out and ruining the aluminum threads. Heres a neat way to use a battery and a welder.
Help please stainless steel bolts stuck in aluminum casting LoginJoin. This thread is both interesting and educational. To better understand I researched stainless bolts in aluminum.
Not surprised that the stainless bolts are not coming out of the aluminum due to the two dissimilar metals and galvanic. Heat the part not the bolt so the metal expands away from the bolt. But use caution as aluminum doesnt give off visual cues for heat.
Hold it on too long and it will just melt. You might want to crunch the numbers including whatever your time is worth and see if simply replacing the part might be better. When a bolt is stuck in an aluminum block you need to try various methods.
A set of bolts that is too close or otherwise forced becomes hard to remove may cause them to break. To get those bolts out you should know what youre doing and have plenty of experience as well as guidelines and patience. Help please stainless steel bolts stuck in aluminum casting LoginJoin.
We should take the jet ski to Michigan my wife said. Its a 2005 with 36 hours and hasnt been run in at least 5 years. Theres a really long story that involves 8 trips to the hardware store 6 trips to.
Brian Brenner of Green Hat Kiteboarding demonstrates how to remove a seized bolt in an aluminum foil mast. Steel screws usually corrode in their aluminum thread holes if assembled dry when water is present. You can ruin the head of the screw with no result.
However giving the screw a whack with a hammer before you unscrew it usually solves this problem. This worked good for me on several machines in the past 20 years. Remove a stuck bolt in aluminum with Nitric Acid.
I went on the internet and looked into a chemical way to remove the steel because I had seen some stuff about accelerating rust on steel with alum before. That was from the bolt when I stuck it in to check out the depth. DSC_0493 by mrsatangto on Flickr Its clear all the way to.
Stop heating the bolt when the bolt head glows a dull orange. Allow the bolt to cool naturally back to room temperature. Place the wrench on the head of the bolt and attempt to loosen the corroded bolt.
If the bolt does not move repeat Steps 5 and 6 until the bolt works free of the aluminium part. In the event its a steel item in aluminum Ill use some alum and soak it to eat out the steel. Apparently aluminum sulfate eats steel but not aluminum—– I have a couple complete sets of the Irwin Bolt-Out sockets.
One of the best tools I have for a specific use. If you have mig or tig drop a bigger nut over the bolt head and weld down through the center to the bolt fill the nut center with weldLet the weld get cold then weld a blob on top of the center and while this is still hot turn out the boltBy letting the first weld cool you have expanded the bolt in the aluminum and let it contract again which should break the bond between the steel bolt and the aluminum the second small weld will work the joint further dont just back the bolt.